Welding is the most important process in shipbuilding. Do you want to know why?
Because welding, as a process, is used in every single step of building a ship. Thus, it is considered the most defect prone process in shipbuilding.
For those working for Ship Design companies, it all starts at with Basic Design documentation related to Welding:
Welding Table
When structural scantling is completed, and you have all the necessary information regarding materials grades, size and thickness, you need to know how to connect them.
Here’s when the Welding table comes in to help you with info on:
– joint design (butt, tee, corner, lap) and edge preparation;
– weld type (butt, fillet, edge, slot);
– size of welds.
Welding details, welding processes and weld size must always comply with the Classification Society requirements for that particular type of ship.
You may not know it yet, but a considerable share of responsibility falls on the shoulders of the ship design engineers.
If you’re wondering how come, the answer is: because they are in charge of joint design and edge preparation.
During the years I spent working on the shipyards I saw many designs that were accurate from the structural point of view but weren’t production-friendly at all.
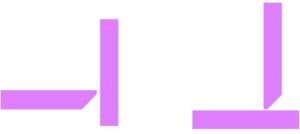
Take for instance the choice of an overhead position instead of a horizontal one. Choosing the right welding position in the design phase can substantially decrease the number of errors in welding execution.
Another example could be the incorrect interpretation of the Classification Society’s requirements.
One of the most common errors is using fillet welds in places where full penetration weld is required (like plates forming boundaries to the sea below Summer Load Line).
NOTE
All engineers in Hull Design department usually define a minimum theoretical design throat thickness.
They offer this information thought: drawings, welding design standard, or specific note for the ship.
Weld process and corresponding penetration is not taken into account.
Test your knowledge:
Q: Do you know what partial penetration butt weld is?
A: Fillet weld used for connecting parts where the fusion faces form an angle smaller than 60°.
On a funnier note:
Q: How many welders does it take to screw in a light bulb?
A: Nobody knows, it’s not in their job description.